

Now let’s take a look at the L298N motor driver pinout in this picture down below and talk about it in detail. L298N Motor Driver Specifications L298N Motor Driver Pinout

To know the technical specifications for the L298N motor driver take a look at the table down below. L298n Motor Driver L298N Motor Driver Specifications L298N module is capable of driving motors with voltages between (5-35)V and up to 2A maximum current which is ideal for DC motors. The L298N Motor Driver is a controller chip with dual H-Bridge which allows controlling the direction and speed of up to 2 DC motors easily at the same time. Dc Motor Direction Control Using H Bridge L298N Motor Driver In the picture down below you can see how in detail how the direction will be changed.
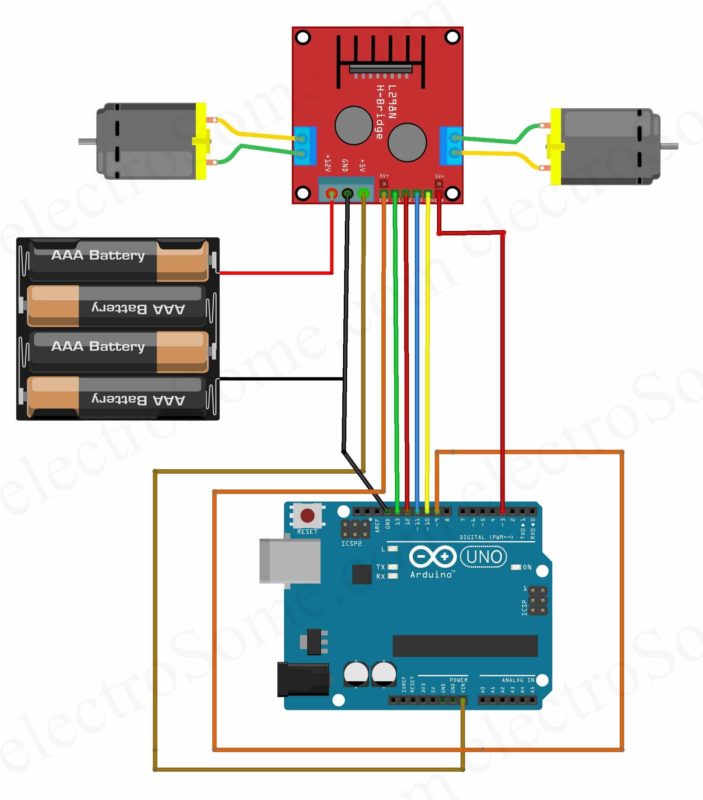
H-bridge consists of 4 switches in the shape of the character ‘H’ and the motor is placed at the center, so we can control the rotation direction by closing the (S1, S4), and opening the (S2, S3) switches and vice versa, so the polarity will be reversed and rotation direction will be changed. H-Bridge is a method that allows us to control the DC motor rotation direction by changing the polarity of the input voltage so the current that flows through the motor will be reversed by using 4 switches. Dc Motor Speed Control Using PWM DC Motor Direction Control Using H Bridge

In the picture down below we apply this method in different Duty Cycle so you can see the difference of average input voltage with each Duty Cycle percentage. So let’s just say you need to rotate the DC motor at the maximum speed so you need to apply 12V average input voltage to do that you need to set the Duty Cycle at 100% percentage. The Duty Cycle is a series of on-off pulses, so to increase the motor speed you need to apply a higher average input voltage as result higher duty cycle percentage, and to decrease the motor speed you need to apply a lower average input voltage as a result lower duty cycle percentage. PWM (Pulse Width Modulation) is a method that allows us to control the DC motor speed by changing the average input voltage value by adjusting the on-off pulses series of the Duty Cycle. H Bridge: this method is used to control the rotation direction of the DC motor.PWM: this method is used to control the speed of the dc motor.To control a DC motor you need to control the speed and rotation direction, so there are two methods to do that: Interfacing L298N Motor Driver With Arduino.DC Motor Direction Control Using H Bridge.
